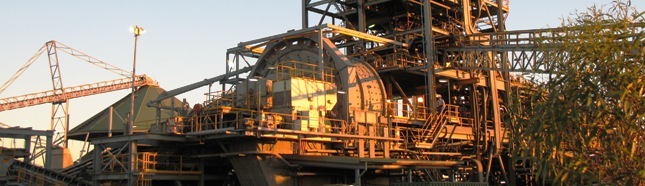
Background
The energy intensity and low efficiency of tumbling mills drives research into optimising their performance. It has been shown that the design of liners and varying mill operating parameters produces changes in the milling action; significantly influencing the throughput and costs of this stage of mineral processing. Another important aspect is that the ball load level has a significant effect on the overall energy consumption of the grinding circuit. The crucial role of size classification in optimising mill utilisation and producing the correct product for the recovery and eventually extractive processes, along with the low separating efficiency of dense particles, motivates research of hydrocyclones and fine screens. The depletion of high grade ores and coarse grained mineralisation has provided good motivation to study mechanisms in fine grinding technologies and identify ways of minimising energy usage and also improve the capacities that can be treated by these devices. Efficient and conservative water treatment has also been identified as a major area of concern that requires addressing. The comminution group has started working on dry processing research programmes with a view to developing circuit options that can improve the usage of plant water. Devices such as the High Pressure Grinding Rolls and Vertical Roller mills have been used in these studies.
Objectives
The overall objective of the research is to improve the efficiency of comminution circuits, while training students in skills useful to the mining industry. Studies of charge motion and subsequently derived realistic mathematical models are the basis of the research. Plant and pilot trials are then used to incorporate real life factors into the mathematically correct frameworks. The research group also conducts plant surveys, using the JKSimMet mineral processing simulator, in order to simulate and optimise current circuit operations.
Integration with the flotation group into a single research centre helps drive the objective to link milling with flotation through multi-component modelling. The potential rewards are immense in terms of cost reduction, higher throughput, and controlling the product. Furthermore, this allows the extractive process to be modelled as a single interactive system so as to optimise the overall operation of the mineral processing plant.
Projects
The research programme has applied research projects aimed at modelling and optimising milling circuit configuration and improving mill performance and design. The inefficient classification of hydrocyclones used for classifying ores of very different densities is also being investigated. Research on fine screens is being undertaken with the view of developing models that can be used to assess the best classification options at the cut size in the region of sub 200µm. Projects targeted with examining the influence of key operating parameters on the performance of dry processing devices, and how these relationships change with different ore types have been commissioned. The wide range of research focus has equipped the group with capabilities to evaluate different circuit options with a view of addressing the challenges of efficient water and energy utilisation.
The Comminution Circuit Modelling programme has initiated several fundamental research projects to analyse the charge motion in rotary mills – with specific reference to grinding action and power prediction – using computational, analytic and experimental techniques. Positron Emission Particle Tracking (PEPT) and high-speed 3D X-Ray filming systems form the basis of the experimental techniques. Investigations into high speeds and volumetric loadings, as well as increased lengths of South African style mills, will be used to extend current models of SAG mills and help steer optimal design. Work is also being done using sensors on industrial mill to study the differences in the toe and shoulder positions with varying mill operating conditions and liner configurations.
The group also provides consultants to MPTech which is the technology transfer wing of the Centre for Minerals Research. The technology transfer services provided include plant optimisation and design studies undertaken using the various tools that have been developed from outputs of research projects within the Centre and from the work performed with collaborating institutions. Comminution courses are also delivered to industrial clients through MPTech. The curriculum of these courses includes training plant engineers in the use of JKSimMet, the application of the simulator to plant optimisation, and on conducting plant surveys.