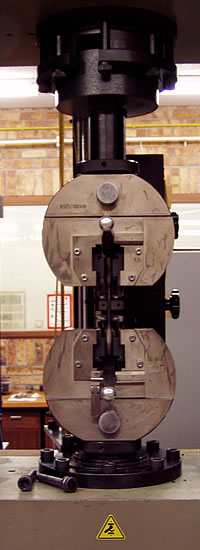
Over the years, the Centre has developed a comprehensive and advanced research infrastructure, supporting the diverse research activities carried out within the Centre. Given our focus on the physical, chemical, electrical, and mechanical properties of ceramic, polymeric, metallic, and composite materials, our equipment base ranges from microscopes for investigating fine microstructures to large mechanical testing systems for evaluating material performance under various conditions.
The Centre is well-equipped with materials testing facilities, both commercially available and custom-built for specific simulation testing. To better manage the vast array of equipment, we have categorised our facilities into the following suites:
Metallographic Preparation: This suite includes equipment for preparing samples for subsequent microscopic analysis, including cutting, grinding and automatic polishing machines.
Microscopy: Our microscopy suite includes several light microscopes, including a Nikon SMZ25 Stereo microscope, Nikon Elipse MA200 Inverted Metallurgical Microscope and a suite of Zeiss Primotech Microscopes for student practicals, and access to the electron microscope suite housed within the Electron Microscopy Unit.
Heat Treatment Furnaces: We offer a variety of furnaces designed for controlled heat treatments, which are essential for studying phase transformations and material behaviour at elevated temperatures. These include standard box furnaces, salt baths with a capacity of 140 C up to 900C, vacuum furnaces with quenching facilities, and one vacuum furnace that can heat to 1500 C.
Thermal Analysis: This suite includes dilatometry, scanning calorimetry, and thermogravimetric analysis (TGA), enabling detailed thermal characterisation of materials.
Hardness Testing: We offer hardness testing capabilities across a wide range of loads (2g – 150kg).
Mechanical Testing: We provide a broad range of mechanical testing machines, including screw- driven testing machines with load capacities ranging from 100 N to 250 kN.
Fatigue Testing: We include two refurbished servo-hydraulic systems with 45kN and 250kN capacities. These systems offer dynamic and fatigue testing capabilities essential for understanding the mechanical performance of materials under cyclic loading. The 45kN frame is also equipped
with a furnace for high-temperature testing.
Impact Testing: Our facilities include pendulum and fully instrumented drop-weight impact testing machines, which are crucial for assessing materials' toughness and impact resistance.
Corrosion Testing: Equipment dedicated to evaluating the corrosion resistance of materials undervarious environmental conditions.
Mini-Casting Facility: A specialised facility for small-scale casting experiments, allowing us to investigate the casting behaviour and properties of metallic materials.
Creep Testing: We possess two load-controlled creep testing rigs, which are essential for studying the long-term deformation behaviour of materials under constant load and temperature.
Thermo-Mechanical Process Simulator: Our Gleeble 3800 is a fully integrated digital closed-loop control system, recently upgraded through an NRF-NEP grant to include state-of-the-art induction heating and a digital image correlation system. The system allows direct resistance and induction heating with rates up to 10 000 °C/sec and maintains steady-state equilibrium temperatures. It is also equipped for high cooling rates, enabling quenching after testing. The mechanical system features a servo-hydraulic system capable of exerting up to 200 kN in compression and 100 kN in tension, with displacement rates as fast as 2000 mm/sec. Our configuration allows for the close simulation of industrial metal processes such as hot rolling,
forging, and extrusion, enhanced by the HYDRAWEDGE module. Additionally, the system supports high-speed heat treatments and welding simulation, making it an invaluable tool for phase transformation studies and advanced materials processing research.
Digital image correlation: We have several digital image correlation systems (MatchID and Dantec), including planer and stereo vision camera setups. We also have a range of digital cameras and lenses that allow a large field of view. Digital volume correlations are performed using volume data from an industrial X-ray micro-computed tomography facility through the Central Analytical Facilities at Stellenbosch University