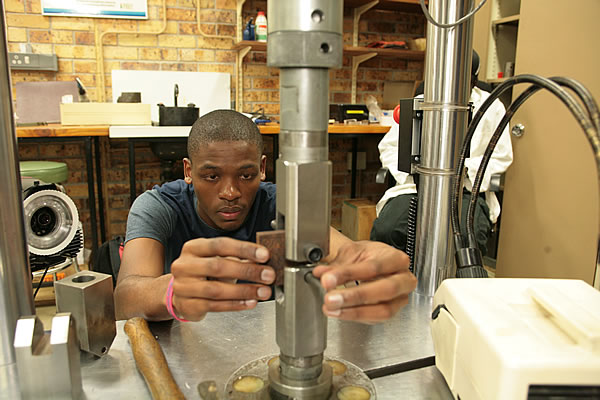
The research activities of the Centre are aimed at addressing national needs in terms of both the provision of technological solutions and the development of skilled graduates. Projects are directed at an understanding of the relationships between the production processes, structure, properties and performance of engineering materials. This encompasses both applied and fundamental work on all groups of materials with special emphasis on metallic materials and is concerned with the improvement in the performance of materials used in engineering systems.
A key focus area is that of thermo-mechanical processing, which includes deformation processing, entailing the development of microstructure during deformation and associated annealing heat treatments. This process, which is integral in many metals producing operations including rolling, forging, extrusion and drawing, is critically important in tailoring the metal microstructures to meet stringent property specifications. Consequently, the successful design of the thermo-mechanical process requires intimate knowledge of the behaviour of the metal microstructure during deformation processing and annealing in order to ensure that the required results are achieved in terms of both product shape and properties. In a similar way, the enhancement of metal properties through microstructure manipulation requires necessary adjustments to thermo-mechanical process parameters in order to evolve the relevant microstructure. With regard to the latter, the Centre for Materials Engineering at UCT provides a crucial supporting role to the national Titanium Centre of Competence in which our role focuses on the optimisation of titanium alloy properties through the process of tailoring the metal’s composition and microstructure. Key to the development of the latter is the thermo-mechanical processing of the metal in such a way that the bulk shape and internal microstructure (or nano-structure in some cases) are modified to meet the end-user requirements. Consequently, the study of the relationships between thermo-mechanical process and metal structure evolution is important.
The study of these relationships between deformation processing and microstructure evolution requires simulation of the deformation conditions and characterisation of the resultant microstructures. Whilst the deformation simulations are able to be performed using our new state-of-the-art Gleeble 3800 thermo-mechanical process simulator, the application of advanced electron microscopy techniques is critical to the successful microstructure characterisation. Electron microscopy offers the ability to apply a broad range of techniques to characterise materials’ structure which may extend from the assessment of the topological arrangement of grains in a polycrystalline material on the one hand to the examination of crystal structure and crystal interfaces at the atomic level. Just as the availability of state-of-the-art instrumentation is vital to the successful use of electron microscopy in performing advanced research in materials science, so too is the availability of expert skills in the application and development of electron microscopy techniques. These skills are best realised by providing training within the context of materials development, which in the present case translates to the analysis of complex microstructure evolution during deformation processing and annealing of metal alloys.
Current research interests at the Centre for Materials Engineering at UCT are aimed at addressing the need to develop competitive niche areas in the production and application of light metal alloy products for the transport, medical and chemical industries. Our activity is critical in underpinning the Department of Science and Technology’s thrust in titanium which has recently resulted in the establishment of the national Titanium Centre of Competence (TiCoC). The broad aim of the TiCoC is to establish a vibrant titanium industry in South Africa that will capitalise on the mineral and energy resources in South Africa and lead to significant value-added product development and manufacture for the international market. Similarly, our involvement with aluminium and magnesium alloys supports the objectives of the Light Metals Development Network promoted by the Advanced Metals Initiative. Furthermore, projects which focus on aluminium and stainless steel are directly aimed at supporting our existing local metals producing industries. An additional important objective of this proposal is to integrate postgraduate students into cutting-edge research projects in physical metallurgy; and by doing this, to develop human capital while generating new knowledge. The proposed project will provide a number of fundamental Materials Science research questions which will motivate the use of new advanced electron microscopy analytical techniques and hence achieve the dual purpose of developing new metals and processes and the application of electron microscopy with high level training of postgraduate students.
The Centre is involved in the development of new metal alloys, polymers, ceramics and hard materials in co-operation with the materials manufacturing industries, and the optimum choice of these materials for the mining, marine, agricultural, processing and energy-producing sectors of South Africa. In this way, research undertaken is not constrained by any particular theme, and academic staff are able to initiate new research areas provided that reasonable expertise and appropriate facilities exist. Consequently, interested parties (both local and international) are encouraged to contact us to discuss collaborative research in most fields of materials science and engineering.